수송기기 산업에서 경량화는 오래 전부터 거론되어 온 핵심 주제이다. 가벼운 무게만을 목적으로 삼아서 플라스틱으로 차량의 모든 부품을 대체할 수는 없기 때문에 금속과 수지를 결합한 이종(異種) 소재 부품 개발이 두각을 나타내고 있다. 금속과 플라스틱은 기존 방식에 의해 나사, 접착 본드, 테이프 등으로 접합할 수 있다. 기존의 이 방식들은 늘어나는 공정과 후속 공정으로의 부품 이동시간, 반제품 및 재공품 증가, 접합 작업시간을 증가시키므로 일체화 성형을 위한 새로운 기술이 필요하다.
접합원리
금속과 수지를 하나의 공정에서 결합시키기 위해 금속 표면처리 기술과 사출성형 기술 융합이 가능하다. 이 방법은 금속 표면에 미세 요철 구조를 만들고 이 금속을 금형에 삽입한 후 사출된 용융수지가 요철 구간을 감싸도록 하는 것이다. 수지(resin)는 미세한 틈을 채워야 하므로 유동성이 좋아야 하고, 금속과의 접합 성능이 우수해야 한다. 금속표면의 미세한 요철은 충진된 수지가 떨어지지 않도록 강하게 붙들어매는 앵커 역할을 수행한다. 사출성형은 용융수지가 금속 인서트 표면의 나노 또는 미크론 크기의 요철 부위를 차고 들어가도록 충진시킨다. 아래 그림에서 (a)는 화학 에칭으로 금속 표면에 요철 형상을 가공한 확대 단면이고, (b)는 용융수지가 성형되는 과정이다.
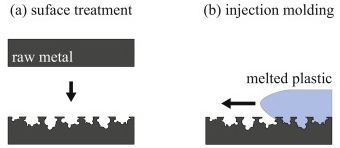
금속표면처리 원천특허는 일본이 보유하고 있으며 오래 전부터 NMT(Nano Molding Technology)라는 명칭으로 기술 상용화를 시도했다. 아래 사진은 NMT의 화학 에칭 기법으로 알루미늄 표면에 미세한 요철을 생성시킨 전자현미경 확대사진이다. 왼쪽은 약품 처리 전, 가운데는 약품 처리 후의 알루미늄 표면 사진이고, 오른쪽은 수지와 결합되어 있는 인서트 사출성형품의 단면 확대 사진이다.(위 연한 색이 수지, 아래 거친 모양의 진한 색이 알루미늄) 요철의 크기는 nm로 상당히 작다.
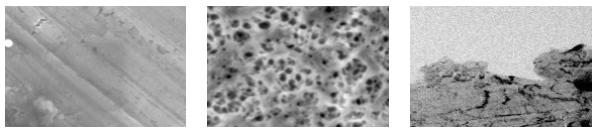
응용
현재 실용화 분야는 MP3 및 스마트폰 케이스와 ECU(Electronic Control Unit)가 있다. 대만의 HTC사에서 최초로 NMT 기술을 스마트폰 케이스에 적용하였으며, 애플사에서 아이폰의 알루미늄 바디에 응용했다. 아래 사진은 2007년 삼성전자에서 NMT 기술을 적용해서 생산한 MP3(YP-10)와 자동차 부품인 ECU이다.
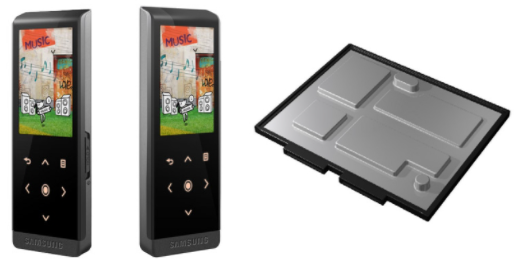
표면처리
금속에 미세 구조를 형성하는 방법에는 화학적 에칭 외에 레이저 가공과 마이크로 블러스트 등이 있다. 이 중에서 미세 구조의 크기는 NMT가 가장 작고 표면처리 가공속도가 제일 빠르다. 극도로 작은 미세 요철 부위에 용융수지를 제대로 채워야 우수한 접합력을 확보할 수 있다. 충진 효율을 좋게 해서 강력한 접합결과를 얻기 위해 수지온도와 금형온도를 높게 하고 사출압력을 크게 설정하는 것이 유리하다. 사출속도의 경우 화학에칭인 나노 요철 크기에서는 작을수록, 물리적 가공인 레이저나 마이크로 블러스트의 미크론 크기에서는 큰 것이 접합력에 좋다는 연구결과가 있다.
금속과 수지의 선팽창계수가 다르므로 사출성형 냉각 과정에서 두 소재의 수축 크기가 다르게 나타난다. 붙어있던 두 소재의 냉각수축 차이는 뒤틀림과 변형을 유발하고 접합강도에 영향을 미칠 수 있으므로 적절한 금형온도 조건과 냉각시간 설정이 중요하다. 이종접합을 위한 플라스틱 재료는 금속접합용 전용 수지를 사용한다.
가전 및 모바일 분야에서 벗어나 경량화 과제를 풀어야 할 자동차 산업에 금속 수지 접합 기술을 확대 적용해야 할 시점이다.