사출성형품의 최종 외관품질 수준을 결정하기 위해서는 반드시 제조자와 수요자가 한도 샘플에 합의하여 양산 준비를 위한 품질 평가 기준을 만들어야 한다. 완벽한 사출성형품의 외관이란 존재하지 않기 때문이다.
사출공정
사출성형의 웰드라인, 플로마크, 변형, 광택 불균일 등 결함 한계를 관계자 모두가 인정하고 있다. 사출성형품 외관에 결함이 존재하는 근본적인 원인은 공정을 제어하는 기술이 불안정한 것에 기인한다. 다양한 공정 변수들을 뚜렷하게 수치적으로 제어하는 방법이 있으면 품질이 완벽하고 일정한 수준의 제품을 제조하는 것이 가능하지만 불행하게도 사출성형공정은 그러하지 못하다.
금형온도
제어가 어려운 대표적인 사출성형 공정변수는 금형온도이다. 온도관리는 플라스틱이 사출산업에 도입되고부터 지금까지 풀어야 할 과제로 남아 있다. 이에 연관된 품질 불균일은 어쩔 수 없는 문제로 받아들여지고 있다.
1970년대까지는 성형온도가 낮은 범용수지를 주로 사용했기 때문에 금형을 빨리 냉각하는 것에 초점을 맞추었다. 1980년대에는 생활가전 시장이 활성화되면서 외관을 중시하는 ABS의 폭넓은 사용으로 금형온도를 상승시키는 것이 성형에 유리하고 외관품질을 향상시키며 응력균열을 방지하는데 도움이 된다는 개념이 도입되었다. 1990년대에 들어서부터 PC등의 고내열성 플라스틱과 PPS, PEEK, LCP(액정수지)등의 엔지니어링 플라스틱이 등장하면서 금형온도를 200℃ 이상으로 가열해야 하는 필요성이 발생했다. 또한 환경보호 이슈와 함께 무도장 무결함 외관을 확보하기 위한 사출성형 방법이 핵심기술로 인정받기 시작했다. 그러나 실제로 금형온도를 200℃까지 가열하는 것에 어려움이 많고, 열팽창에 의해서 금형작동부에 문제가 발생하며 충진완료 후 성형품이 금형에 달라붙어 있어 취출이 원활하지 않은 부적합 요소가 존재했다. 높은 온도로 인한 파팅 Burr, 수축 발생도 큰 문제로 인식되었다.
가설
실제로 금형을 우리가 원하는 온도인 200℃ 이상으로 가열하면 어떤 현상이 일어날까. 가설만 세워놓고 실제로 해 보지 않으면 검증할 수 없다. 실제 현상을 알아야만 지금까지 낮은 금형온도로 성형하는 방법이 얼마나 많은 문제를 야기하는지를 이해할 수 있다. 일반적으로 금형온도가 높으면 수축이 기대치보다 커지고 표면광택이 크게 좋아지는 것으로 언급하는 경우가 많은데 초고온 급속가열 급속냉각 사출성형 과정에서 확인한 결과 일부는 보완이 필요한 가설임이 밝혀졌다. 초고온으로 금형을 가열하면 다음과 같은 현상이 발생한다.
- 금형온도가 220℃일 때는 120℃일때보다 사출압력 30~40% 감소
- 금형온도가 220℃일 때는 40℃일때보다 사출압력 50~60% 감소
- 게이트로부터 충진 말단부까지 도달하는 용융수지의 압력 손실이 50% 이상 대폭 감소
- 성형품의 표면밀도 향상
- 성형품 표면의 기포 발생 제거
- 미세패턴의 완벽한 전사
- 웰드라인, 플로마크, 게이트마크, 제팅 불량 제거
초고온 사출성형은 금형온도가 사용 수지의 열변형온도 이상으로 유지되어 웰드라인이 보이지 않고 도장이 불필요하다. 이 방법을 사용하면 뚜렷한 색상 구현이 가능해져 OA기기 및 생활가전, 자동차 인테리어 외관 부품에 폭넓게 응용할 수 있다. 금형온도 상승은 금형표면과 용융수지의 밀착성을 한층 강화시켜 광택도를 개선시킨다.(일반금형 대비 5~10% 상승) 또한 강도 보강을 위해 강화섬유가 첨가된 수지를 사용할 경우 섬유층의 표면 배향을 억제시켜서 비교적 깔끔한 외관 확보가 가능해진다.
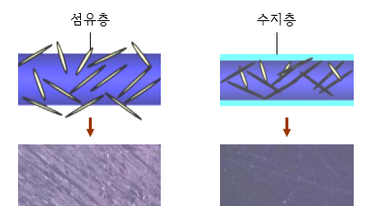