드로잉가공(drawing)은 소재(블랭크)를 다이에 올려놓고 강한 힘으로 눌러 용기 모양의 제품을 만드는 가공이다. 제품은 바닥이 있고 이음매가 없으며 원통 및 각통 형상의 용기이다. 소재에 하중을 가하면 원주 방향으로는 압축이, 반지름 방향으로는 인장이 진행되면서 소재 중심부가 다이 속으로 유입된다.
드로잉률
드로잉률(m)은 블랭크 직경(D)과 용기 직경(d)의 비로 나타내는데 드로잉률이 너무 작으면 높이가 큰 제품을 가공하는 것으로 가공량이 커서 파단 가능성을 내포한다고 볼 수 있다.
드로잉률 = 용기 직경 / 블랭크 직경
재드로잉률 = 가공완료 용기 직경 / 가공직전 용기 직경
드로잉비 = 블랭크 직경 / 용기 직경
파단을 일으키지 않고 가공할 수 있는 최소드로잉률을 한계드로잉률이라고 하는데, 이 값이 작을수록 우수한 드로잉 가공성을 보인다. 2차 이상의 재드로잉을 하는 경우 가공경화가 일어나므로 재드로잉률은 일정하지 않고 드로잉 횟수가 증가할수록 가공성이 점차 감소하는 경향이 있다. 이 경우 연화풀림 열처리를 하면 드로잉 가공성을 개선할 수 있다. 드로잉비는 드로잉률의 역수로 가공의 난이도를 나타내는 기준이다.
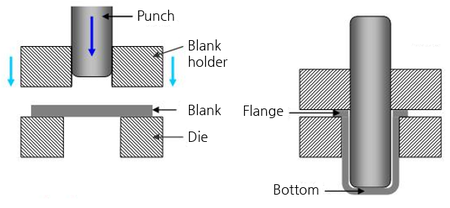
아이어닝
드로잉 가공은 압축, 인장, 굽힙이 부위별로 다르게 작용하므로 용기 두께에 편차가 발생한다. 이 영향으로 두꺼운 부분은 주름이, 얇은 부분은 균열이 생기기 쉽다. 대개의 경우 두께와 외경 치수를 일정하게 맞추기 위해 펀치와 다이 사이의 클리어런스를 작게 하여 다시 드로잉하는 아이어닝(ironing) 공정을 거치게 된다. 원통 용기에서의 아이어닝 클리어런스 크기는 재료 두께의 1.1~1.2배이다. 드로잉 가공은 주름과 균열을 발생시키는 경우가 많은데 안정적인 가공을 위해서는 블랭크 홀더(blank holder)의 역할이 중요하다. 블랭크 홀더가 누르는 압력은 플랜지부에 나타나는 주름을 억제하는 동시에 마찰력이 생성되어 재료가 다이 속으로 들어가는 것을 방해하기도 한다. 블랭크 홀더 압력이 너무 크면 과대한 마찰력으로 균열이 발생할 수 있으므로 소재와의 밀착 정도를 조정하여 해결할 수 있다. 균열이 생기면 블랭크 홀더와 소재 사이 공간에 라이너를 삽입하여 간격을 벌려 누르는 힘을 감소시키고, 주름이 생기면 라이너를 제거하여 간격을 줄여준다.
블랭크 홀더가 효과를 나타내려면 소재와 블랭크 홀더 접촉면의 표면거칠기가 좋아야 한다. 균형잡힌 밀착을 유지하기 위해 경사진 부분이 없이 평탄해야 소재를 누르고 있는 압력이 치우침 없이 균일해진다.
다이 안으로 들어가는 재료의 유입 저항이 부분적으로 다르게 나타나면 주름과 균열을 동시에 일으킨다. 미리 준비해 놓은 소재에 버가 있으면 블랭크 홀더와의 접촉에서 틈새가 만들어져 주름이 발생한다. 가공전 블랭크 소재의 품질관리가 필수적이다.
금형의 평행도가 나쁘면 블랭크 홀더의 접촉면 확보가 불안해지고 금형 수명에도 영향을 미친다. 상형과 하형의 수직 운동이 부드럽게 반복되도록 정밀도 높은 금형을 제작하는 것은 필수이다.
블랭크 홀더 압력은 드로잉 압력의 20%~50% 정도이다. 드로잉비가 클수록(드로잉률이 작을수록), 재료의 변형저항이 클수록, 재료 두께가 얇을수록, 플랜지부의 윤활성이 좋을수록 더 큰 블랭크 홀더 압력 설정이 필요하다.
곡률반경
펀치와 다이의 곡률 반경 윤활성이 동일하게 좋으면 가공에 필요한 힘을 제대로 발휘하지 못한다. 두 지점의 윤활성을 다르게 하는 것이 주름 발생을 억제시키므로 펀치쪽 곡률 반경의 윤활을 다이쪽보다 나쁘게 하여 차이를 두는 것이 좋다. 펀치와 다이의 곡률 반경이 크면 가공성은 좋아지는 반면 주름이 생기기 쉽고, 곡률 반경이 너무 작으면 과도한 굽힘과 수축을 동반하여 균열이 일어나게 된다. 적절한 크기의 곡률 반경 설정이 필요하다.
드로잉 속도가 빠르면 균열이 발생하므로 적합한 속도의 가공조건을 확보해야 한다. 쿠션핀은 펀치 가까이 오도록 배치하고 길이 편차가 없도록 해야 한다. 쿠션핀 길이가 다르면 힘이 작용하는 균형이 깨져 주름과 균열이 발생하기 때문이다.
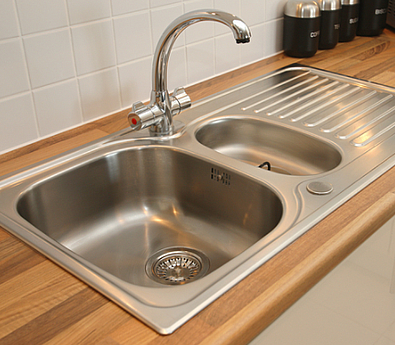