일정 기간 사용한 드릴은 마모나 치핑이 누적되어 절삭성능이 급격히 떨어진다. 재연삭을 하거나 교체를 하려면 적당한 시점을 판정하는 기준이 필요하다. 드릴 수명을 판정하기 위한 대표적인 기준은 다음과 같은 7가지 항목이 있다(우선순위로 나열).
- 가공한 구멍의 합산 수량으로 교체시점을 판정
- 공구 마모량으로 교체시점을 판정
- 가공한 구멍의 정밀도와 표면거칠기 상태로 교체시점을 판정
- 절삭저항이 증가하는 현상으로 교체시점을 판정
- 절삭칩 형상의 변화로 교체시점을 판정
- 절삭칩 색깔의 변화로 교체시점을 판정
- 절삭진동과 절삭소음으로 교체시점을 판정
절삭온도
가공 경력자라 하더라도 공구 수명을 판정하는 일은 결코 쉽지 않다. 판정에 앞서 공구 성능을 오랫동안 유지하고 수명을 연장시키는 것이 중요하다. 가공조건 가운데 절삭속도(m/min)와 이송(mm/rev)은 드릴 수명과 직접적인 연관성을 가지고 있는 중요한 요소이다. 절삭온도는 절삭속도와 이송 크기에 비례하고 이로 인해 발생하는 절삭열은 공구의 마모를 촉진시켜 드릴 수명을 단축시키는 요인으로 작용한다. 그림에서 절삭속도와 이송이 커질수록 절삭온도가 상승하고 가공할 수 있는 구멍의 수량이 급감(드릴 수명 단축)하는 것을 볼 수 있다.
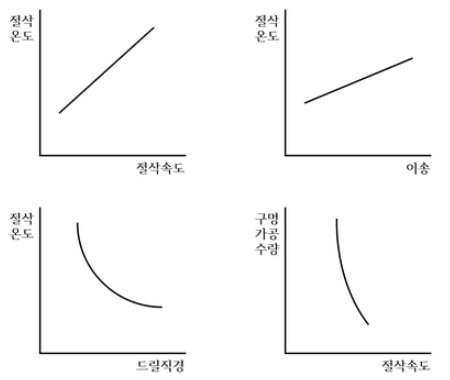
이송속도
이송속도는 이송과 RPM에 연관되어 있다. RPM이 일정한 조건에서 이송속도를 크게 하면 이송도 크게 되고 절삭열이 발생하여 절삭온도를 상승시키므로 드릴 수명이 짧아지게 된다. 이송속도가 너무 크면 비틀림 파괴 및 좌굴이 일어나서 드릴이 부러지게 된다.
이송속도(mm/min) = 이송(mm/rev) x RPM(rev/min)
이송속도 : 분당 구멍뚫기 거리
이송 : 드릴 1회전당 움직인 거리
RPM : 분당 드릴 회전수
공구수명
드릴 직경이 크면 드릴 체적도 커지므로 많은 양의 열을 받아들일 수 있다. 큰 직경을 사용한 절삭가공에서는 날끝에서 발생하는 열이 드릴 쪽으로 빠르게 이동하여 절삭열을 낮추는 냉각효과가 일어나는 것으로 볼 수 있다.
가공경화성이 큰 단단한 재료는 드릴 선단각을 크게 하여 절삭깊이를 크게 잡는다. 이는 조금이라도 가공경화의 영향을 받지 않는 곳을 절삭하여 공구 수명을 늘리기 위한 목적이다.
피삭재 경도 또한 드릴 수명에 영향을 미친다. 동일한 재질에서 미세한 경도 차이가 존재하면 가공성이 균일하지 않아서 공구 수명은 큰 격차를 보인다. 동일 재질을 대량 가공하는 경우 공구수명 관리 차원에서 재료의 허용 가능한 경도 편차를 미리 설정해 두어야 한다. 금형강을 생산하는 제조업체는 품질을 증명하기 위해 금형강 표면 여러 부위의 경도를 측정한다. 각 부위의 경도 편차가 오차 범위 안에 들어와야 한다.
초경 드릴은 고온에서의 내마모성이 우수하고 정밀도가 높은 구멍뚫기를 할 수 있지만 치핑, 깨짐, 열충격에 약하다. 공구 수명을 길게 유지하기 위해 이송을 작게 하되 이로 인한 능률 저하는 빠른 절삭속도로 극복하도록 가공조건을 조정하도록 한다.
또한 비수용성 절삭유를 사용하는 것이 수용성 절삭유를 사용하는 경우보다 공구 수명을 연장시키는 효과가 있다.
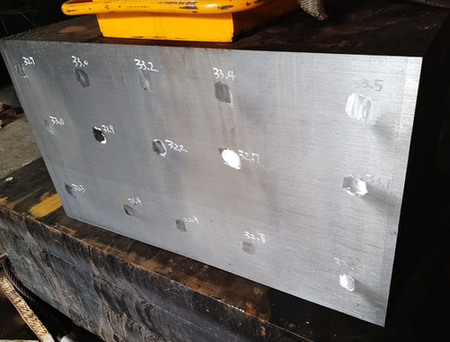