플랜지 형상이 없고 용기 바닥 모서리에 굽힘 반경(r)이 있는 블랭크의 직경(D)은 다음 식으로 구한다.
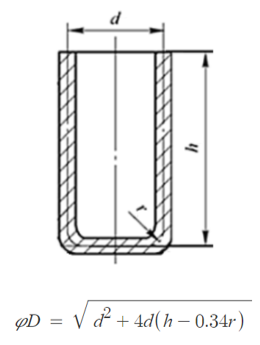
D : 원형 블랭크 직경(소재크기)
d : 용기 내경(두께 중심부 기준)
h : 용기 높이(두께 중심부 기준)
r : 용기 바닥(펀치)의 모서리 곡률 반경
수식 뒤 부분에 있는 (4×0.34r)은 바닥 모서리가 직각이었을 때의 직선부 면적을 계산한 후 r이 있을 때의 반경에 해당하는 면적을 감안한 값이다.
드로잉 비율
깊은 용기는 2회 이상 재드로잉이 필요한 경우가 있는데 직경이 감소하는 한계 비율은 아래 표와 같다. 맨 처음에 나와 있는 숫자 0.63은 (T/Dx100)이 0.08~0.15 범위 내에 있는 경우 Ø100인 블랭크를 1차 드로잉했을 때 최소 직경을 Ø63까지 가공할 수 있다는 것을 의미한다. 2차 드로잉을 하면 용기의 최소 직경은Ø51.66(Ø63×0.82), 3차 드로잉을 하면 가공 가능한 최소 직경이 Ø43.39(Ø51.66×0.84)가 된다. 즉 Ø100 크기를 3번 드로잉하면 최소 Ø43.39까지 만들 수 있다. 드로잉 횟수가 증가하면 가공경화가 일어나서 가공성이 저하되는 경향이 있다.
블랭크 두께와 직경의 비율(T/Dx100) | ||||||
---|---|---|---|---|---|---|
공정순서 | 0.08~0.15 | 0.15~0.3 | 0.3~0.6 | 0.6~1.0 | 1.0~1.5 | 1.5~2.0 |
1공정 | 0.63 | 0.60 | 0.58 | 0.55 | 0.53 | 0.50 |
2공정 | 0.82 | 0.80 | 0.79 | 0.78 | 0.76 | 0.75 |
3공정 | 0.84 | 0.82 | 0.81 | 0.80 | 0.79 | 0.78 |
4공정 | 0.86 | 0.85 | 0.83 | 0.82 | 0.81 | 0.80 |
5공정 | 0.88 | 0.87 | 0.86 | 0.85 | 0.84 | 0.82 |
용기 내경이 줄어들게 되면 그에 따른 높이를 위 식으로부터 구할 수 있다.
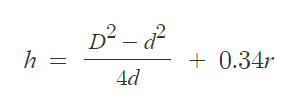
다음은 내경(d) Ø46, 깊이(h) 40mm, 용기 바닥 모서리 반경(r)이 5mm인 플랜지 없는 용기의 블랭크 크기를 계산한 예이다. 블랭크 두께는 1mm이고, 높이에 대한 트리밍 여유값은 2mm이다. 드로잉 후 트리밍으로 2mm를 잘라내는 공정을 따르는 경우이다.

T/D(1/97.2)는 1.03이므로 1차 드로잉의 한계 직경은 Ø51.5(97.2×0.53)이고, 2차 드로잉의 한계 직경은 Ø39.1(51.5×0.76)이다. 제품 직경은 Ø46이므로 1차 드로잉 한계 직경보다 작고, 2차 드로잉 한계 직경보다 크기 때문에 2번의 성형공정을 거치면 된다. 금형 제작에서는 1차 펀치를 Ø55와 r8.5, 2차 펀치를 Ø46과 r5로 설정하면 각 공정에 따른 드로잉 비율은 0.57(55/97.2)과 0.84(46/55)가 되므로 한계 직경보다 커서 무난한 가공을 수행할 수 있다. Ø55인 1차 펀치를 사용해서 가공할 때의 제품 높이(h1)는 32.08mm가 되고, 2차 펀치에서는 42mm가 된다. 2mm를 트리밍 가공해서 최종 제품 높이를 40mm로 맞춘다.
