다이캐스팅 기계는 대표적으로 핫챔버(Hot chamber)와 콜드챔버(Cold chamber)로 구분된다. 핫챔버의 경우 주로 주석, 아연, 납 등의 용융점이 낮은 합금의 주조에 사용되며, 콜드챔버는 구리, 마그네슘, 알루미늄합금 등 비교적 용융점이 높은 비철금속 합금 주조에 이용되고 있다.
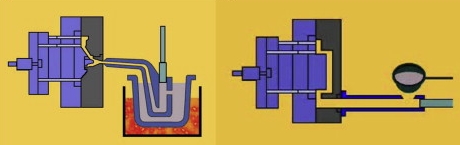
콜드챔버
콜드챔버는 국자(Ladle)로 용탕을 숏슬리브에 공급한 후 플런저로 밀어 사출하는 형식이다. 낮은 온도에서 유동성이 나쁜 합금을 고압으로 금형에 밀어넣는다. 용탕과 사출부가 분리되어 있어 주조압력을 높일 수 있기 때문에 치밀하고 균일한 조직을 만들 수 있다. 두께가 두꺼운 중대형 부품 제조에 많이 사용한다.
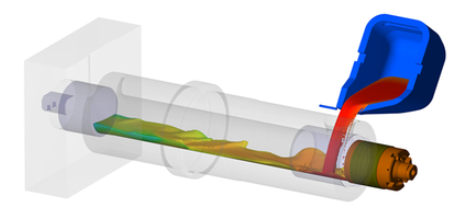
핫챔버
핫챔버는 사출실린더와 용해로를 내장하여 유동성을 좋게 한 후 거위목(Goose neck)이라고 불리는 입구를 통해 낮은 압력으로 일정량의 용탕을 사출하는 형식이다. 구스넥 인젝션 방식이라고도 한다. 용탕의 열손실이 거의 없이 금형에 주입된다. 콜드챔버의 숏슬리브(Shot sleeve) 안에서 일어나는 공기 유입과 산화물 발생을 줄여주기 위해 용탕온도를 식지 않도록 하는 구조로 이루어져 있다. 핫챔버 방식은 낮은 용융점을 갖는 합금재료로 작은 크기의 부품을 주조하기 때문에 응고시간이 길지 않아서 성형사이클이 짧고 생산성이 좋다. 하지만 뜨거운 용탕이 거위목과 계속 접촉하고 있어 부품 수명이 단축되는 단점이 있다.
구분 | 콜드챔버 | 핫챔버 |
---|---|---|
장점 | ○ 중대형 부품에 적합하다. ○ 두꺼운 부품에 적합하다. ○ 주조압력을 높힐 수 있다. ○소모품이 저렴하고 교체가 쉽다. | ○ 성형사이클이 짧다. ○ 용탕 온도제어가 쉽다. ○ 공기 유입을 최소화한다. ○ 얇고 넓은 부품 제조가 가능하다. |
단점 | ○ 성형사이클이 길다. ○ 용탕 온도제어가 어렵다. ○ 가스와 산화물이 유입된다. ○ 자동급탕시스템이 필요하다. | ○ 주조압력이 낮아서 두꺼운 제품에 부적합하다. ○ 소모품 가격이 비싸다. ○ 부품 교체에 시간이 많이 걸린다. |
제품 | ○ 중대형 두꺼운 부품(~10kg) | ○ 중소형 얇은 부품(2~3kg) |
참고자료
콜드챔버 – https://www.youtube.com/watch?v=JLfV_u8HRcY
핫챔버 – https://www.youtube.com/watch?v=bzSSfBgkWfc